Industrial food treatment processes need to tackle bacteria that can spoil food. These microorganisms, although non-pathogenic, can make food products unpalatable and affect how long they can be stored for.
Current food preservation techniques rely on temperature or pressure. But researchers in the EU are working on a new method that combines high pressure with temperature, which they hope can produce high quality, fresh food that can be stored for months.
We spoke to Sergio Ramos, at the National Centre for Technology and Food Safety (CNTA) in Spain, who has recently tested the new technique on four food spoilage bacteria – Bacillus stearothermophilus, Bacillus amyloliquefaciens, Clostridium sporogenes and Bacillus coagulans – for the European HIPSTER project.
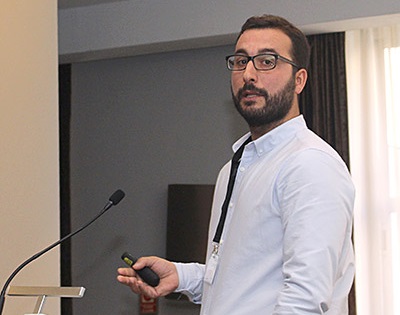
In what conditions do the four bacteria you looked at grow?
These microorganisms are mesophilic and thermophilic, so they can grow at 30 or 55°c. They are spoilage microorganisms – they can spoil food products by producing alterations in colour, texture, and flavour. These organisms are not pathogenic.
Would they grow in most foods?
Yes, they are typical in most foods, for example B. stearothermophilus is a common microorganism in canned foods, so it is common in industrial prepared foods. And B. amyloliquefaciens is a typical soil microorganism that can contaminate food products. The objective of the HIPSTER project is to ensure that we have a process window of temperature and pressure combinations that allow us to reduce the spoilage and the pathogenic microorganism in all the food products.
How do these bacteria end up in our food products?
They are present in the products normally. They come with the ingredients of the food products.
If your food was contaminated with these products would you be able to tell?
Yes. Normally there will be some production of gas, and the consumer can detect abnormal flavours, colours, tastes, or textures. These are the common alterations in food products that these microorganism produce.
In the trials you tested vegetable soup, green peas with ham, braised veal, and tomato soup, why were those four food products chosen?
They are typical food products that one of the companies involved in the project selected. The vegetable products have a lot of spore contamination. So they selected green peas with ham, for example, because it is a mix of vegetable and meat products. And the vegetable soup was selected because it is a mix of vegetables that can present a low level of contamination with the spores.
What were the main results of the recent trials?
The main conclusion is that there is a positive affect from the pressure and temperature technologies acting simultaneously. So we can achieve a reduction in bacteria with this combination in a shorter time, even in a lower temperature process.
The next step is to validate that the combination of pressure and temperature does not produce changes in the product. Thermal treatment has a lot of negative effects on the food products, in texture, flavour, colour and taste. We expect to achieve better colour retention, better texture, better flavour and better taste with the combination of pressure and temperature.
But at this moment the main conclusion is that we can achieve a level of security with the combination of pressure and temperature in shorter times and at lower temperatures.
How much faster can the high pressure and temperature process reduce bacteria count, when compared with current industrial food treatment processes?
Generally the traditional thermal treatment for packaged food products in a retort or open pasteurizer takes near or even more than an hour, including the heating and cooling steps. In the high pressure-temperature process, the fast compression heating and decompression cooling, results in shorter treatment times.
In addition, if a synergistic effect in the inactivation of spores by high pressure and heat compared to inactivation by heat alone is demonstrated, the treatment time required can be reduced even more. Probably between 30 and 50% less, we are now defining it.
Why is it necessary to develop a new food treatment process?
The food industry needs to cope with a globalised and increasingly competitive market. This is why there is a need for novel processes to enhance product quality and shelf life; reduce energy and water usage, minimise waste and improve efficiency to promote competitiveness and sustainability; and assure of safety.
The current thermal preservation methods result in shelf stable food products, with long shelf life but undesirable losses of sensory and nutritional quality. Moreover, the non-thermal alternatives result in better quality products but limited shelf life. The high pressure-temperature process aims to obtain both benefits: long shelf life and high quality food products.
When do you expect the high pressure-temperature technology to be ready for commercial use?
Good question. Maybe in 3-5 years.
By Michael Allen